Announcement
The future is made with industry - and therefore, it is time for an European Industrial Deal:
YES, we as IRLA have signed the Antwerp Declaration!
If this declaration comes into force, it would allow industry to take its responsibility as a key driver towards a sustainable and competitive Europe, that would work for all players involved.
For further information, please have a look at European Antwerp Declaration.
Join the 1200+ organisations supporting the #AntwerpDeclaration. Our upgraded website is your gateway to get involved. Let’s shape Europe’s future together.
Explore more at antwerp-declaration.eu.
#IndustrialDeal
April 2023
POSITION PAPER ON RELEASE LINERS AS PACKAGING UNDER THE CURRENT PPWR1 PROPOSAL – A DETERMINATION YET TO BE MADE
WHAT ARE SILICONE RELEASE LINERS TECHNICALLY? Silicone coated Release Liners are integral components of self-adhesive products. The Release Liner performs a number of essential roles in processing self-adhesive materials, such as process aid during adhesive coating, carrying the self-adhesive material during cutting, printing, die-cutting, and transporting before finally ‘releasing’ the self-adhesive material to be applied at its final point of use. The most common applications are for self-adhesive labels and double-sided tapes are where there needs to be a protective liner up until the point of use, but release liners are also used in a wide range of other self-adhesive applications such as Graphics, medical plasters, and not only with adhesives, but e.g. for bakery use, vulcanizing of rubber, butyl mastics, fibre composites, transfer printing, or casting operations.
WHAT ARE SILICONE RELEASE LINERS IN RESPECT OF THE PPWR? IRLA members manufacture and supply siliconized rolls of both paper and plastic film for subsequent use as release liners for self-adhesive products including carriers for pressure sensitive adhesives (PSA). The coated rolls ‘as supplied’ to the customers of IRLA members are understood to be products in their own right.
Where release liners are used with labels, they can become confused with the packaging onto which labels are often applied. However, the release liner itself is fundamentally a protective provision for the self-adhesive side of the label and is discarded at the point of label application. It can therefore be considered as waste from that point on or, where the label application process is mechanized in industrial or professional settings, it can be considered as a production residue.
In their wider applications in the industrial sector, release liners primarily function as a process aid. They do not display the primary characteristics of packaging, such as containment or presentation of goods. For these reasons, IRLA considers that release liners should be assessed as non-packaging materials. However, because there continues to be uncertainty about this status IRLA asks for clarity in the text of PPWR and its Annexes to make sure that release liners, especially those used in industrial settings, are understood not to be packaging materials.
FINAL REMARKS ON RELEASE LINER RECYCLING IRLA recognizes the importance of the European Union’s Circular Economy Action Plan and the role that its members and their customers will play in facilitating schemes and related recovery pathways to maximize the recycling rates of siliconized sheets. As ISRI2 has already recognized, these products are inherently recyclable when segregated in industrial settings and this is the model anticipated to represent the bulk of future recycling in the sector. However, the industry needs to understand the framework under which its performance will be measured within the EU and the key criteria on which to focus. It is IRLA’s understanding that the provisions of the PPWR are aimed primarily at packaging targeted at the consumer, thereby making its approach inappropriate for release liners as defined herein, whether theoretically considered packaging in some applications or not. Since more than 80% of the products of IRLA members are used in industrial and professional settings, a segregated recycling approach, as identified by ISRI, is the more logical option. The other point of importance to note is that self-adhesive surfaces avoid the widespread use of liquid adhesives, with the waste and potential pollution resulting from that option. Since a ‘zero pollution environment’ is a central goal of the European Green Deal, other European legislation should be sure to avoid jeopardizing that objective by undermining a fundamentally cleaner technology.
IRLA, the International Release Liner Association, was established in 2009. IRLA is the organisation gathering and representing the producers of siliconized release papers and films as well as members of the respective supply chain. For further information please see: https://irla.info
---
1 PPWR - Packaging & Packaging Waste Regulation – Commission Proposal
2 ISRI - Institute of Scrap Recycling Industries
November 2022
The European Packaging Value Chain expresses serious concerns about the European Commission suggested approach on packaging and packaging waste legislation
- Joint industry statement from the Packaging Value Chain -
The European Packaging Value Chain expresses serious concerns with regards to the approach taken by the European Commission in its revision of the EU rules on packaging and packaging waste.
Our industry shares the ambitious objectives of the EU Green Deal and Circular Economy Action Plan 2.0 and is fully engaged in taking action to bring packaging sustainability to the next level. For that to happen, we need a corresponding supporting regulatory framework to help us drive this change further. Over the past years, we have been actively engaging with DG Environment on the revision of this key piece of legislation, sharing our best practices and offering solutions to make this proposal both environmentally and economically successful. Yet despite our efforts, most of our key recommendations for ensuring food and products are adequately protected have not been taken on board. We therefore question whether the proposal is consistent with the ‘Better Regulation’ imperatives, principally whether an ‘evidence-based approach’ has been employed and whether the ‘evaluate-first’ principle has been met. We also believe that the ‘cost-effectiveness’ of various impacts and the ‘proportionality’ of key provision have not been adequately evaluated.
The current approach will lead to a regulatory environment that will be unworkable at best and crippling for whole sectors of the European industry at worst, from agriculture to machinery and from food processing to pharma and cosmetics to electronics, just to name a few, with significant risks of Disruptions in many EU supply chains and for our trade flows. By dismissing the key role of recycling to achieve packaging circularity, it would paradoxically serve to make it harder to convert waste into viable, secondary raw materials that can be used in the market, setting back the cause of recycling while jeopardising millions of jobs and billions of euros of investments precisely at a time when Europe needs resilient and sustainable growth. For many companies, whether packaging manufacturers or users, especially SMEs, the impact of this proposal is not only unsustainable, but also existential.
The proposal risks harming packaging producers, of all materials, as well as their suppliers and their users, in industry, logistics and retail. We call for defining a framework for the rapid adoption of clear Design for Recycling guidelines, to be updated regularly with the involvement of the value chain experts for the different packaging materials. As Design for Recycling guidelines will determine which packaging is allowed in circulation on the Union market, the proposed prescriptive negative lists are not only unnecessary but they will have as a sole outcome that of disrupting innovation and investment in further recycling facilities, with far-reaching environmental, employment and economic consequences. They would also overshadow the industry’s ongoing investments towards achieving packaging circularity through material innovation, increased recyclability, collection and the use of more recycled content. Increased recycling also requires a radical improvement of collection to ensure that packaging is recycled in practice and for new waste streams to become fully operational.
The proposed refill and reuse targets are not realistic, disproportionate and could be counterproductive. Reuse and refill are not always the best option from a climate and environmental standpoint, as many third-party certified LCAs studies have demonstrated, for example because of the additional logistical complexity, in case of long transport distances or wherever recycling and mandatory collection can be efficiently organised. Specific instruments, not foreseen in the proposal, are needed to create a framework for the scaling up of refill and reuse beyond niche projects. Moreover, to our knowledge, there has been no environmental impact assessment indicating how these targets would help deliver a better environmental outcome. Refill and reuse should be required to deliver a better environmental outcome in real life conditions compared with its single-use alternative and be evaluated according to specific criteria, related to hygiene, and food health and safety requirements. Instead of fixed targets, the proposal should set a clear framework to enable mandatory collection and recycling while scaling-up refill and reuse where it makes environmental and ecological sense, and can further strengthen the competitiveness of the Single Market.
To achieve the 2030 recyclability goal requires concrete and collective efforts which go well beyond the packaging design. They require significant investment in sorting and recycling infrastructure to ensure that packaging is collected in the first place. In the absence of this, we will end up with a disparate Member State performance and a more fragmented Single Market.
The proposed mandatory recycled content targets for plastic packaging fail to take account of bottlenecks that affect the availability, quality and cost of recycled plastics. Furthermore, pending the adoption of rules impacting chemical recycling and given the scarce availability of and legal restrictions on recycled polymers that could be included in contact-sensitive applications (e.g. food, pharma, medical and cosmetics products), the proposed targets cannot be achieved without compromising packaging functionality or the use of additional material with a higher environmental impact. Once again, there seems to have been a total lack of assessment into the actual feasibility of such targets. Chemical recycling needs to be effectively counted towards the targets to unlock the necessary investments. In addition, appropriate quantitative safeguards and review mechanisms to adapt the targets, if needed, are necessary to ensure their environmental and economic viability.
The packaging supply chain is constantly working in close collaboration to continue innovating packaging formats to minimise the amount of material needed for packaging to fully perform its functionalities. The proposal is strengthening the requirements to use the least amount of material necessary. However, it then goes further in proposing arbitrary product to pack ratio for specific products without taking into account the packaging’s safety and functionality, nor the different characteristics of the packaged products or why, for example, a sufficient cushioning thickness is necessary to prevent breakage. Equally arbitrary would be to set targets for other product categories, without specific consideration of the different characteristics of the product.
A system is vulnerable if it misses key sustainability principles such as coherence, mitigation, robustness and resilience when legislating. Arbitrary bans and unrealistic and discriminatory targets that are not supported by scientific and empirical evidence do not create the positive investment climate needed to support the transition and they make industry question if to continue investing in this legislative setting is at all sustainable. We want Europe to have circularity rules that set the standard for the rest of the world. Yet, the PPWR as currently drafted will set this process in reverse and may even turn the clock back on aspects of the Green Deal.
We call on the European Commission to address these critical issues and remain at your disposal for further dialogue so that the proposed Regulation is future-proof and delivers a regulatory environment that supports the European industry on its journey towards a fully circular economy.
Signatories
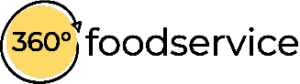
360 Food Service
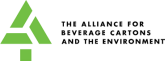
ACE - the Alliance for Beverages Cartons & the Environment
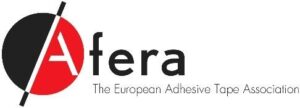
Afera - The European Adhesive Tape Association
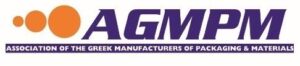
AGMPM - Association of Greek Manufacturers of Packaging & Materials
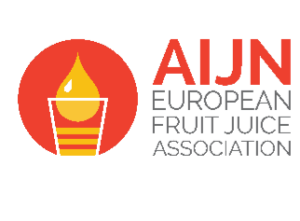
AIJN - European Fruit Juice Association
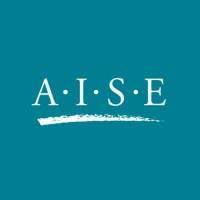
AISE - International Association for Soaps, Detergents
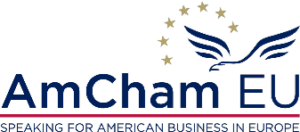
AMCHAM EU
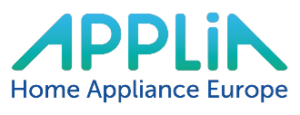
APPLiA - Home Appliance Europe
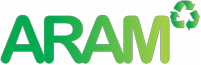
ARAM - Romanian Association for Packaging and the Environment

CEFLEX - A Circular Economy for Flexible Packaging
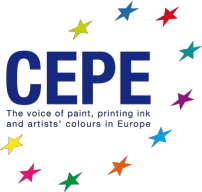
CEPE - European Council of the Paint, Printing Ink and Artists' Colours Industry
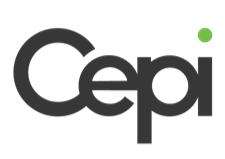
CEPI - Confederation of European Paper Industries
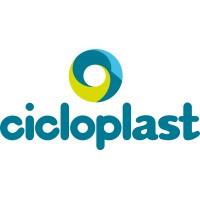
Cicloplast – EPRO

CICPEN
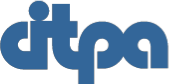
CITPA - the International Confederation of Paper and Board Converters in Europe
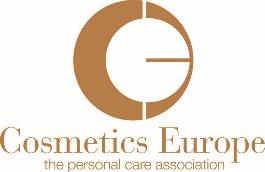
COSMETICSEUROPE
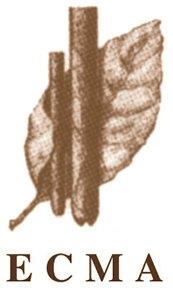
ECMA - European Cigar Manufacturers Association
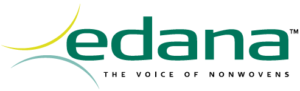
EDANA - International association serving the nonwovens and related industries
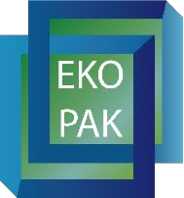
EKO-PAK
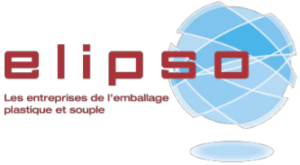
ELIPSO
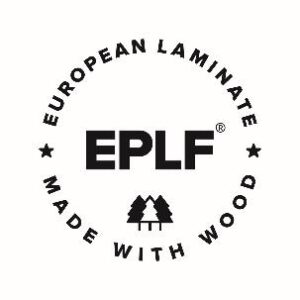
EPLF - European Producers of Laminate Flooring Association
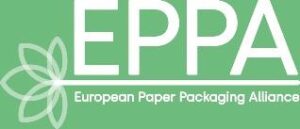
EPPA - European Paper Packaging Alliance
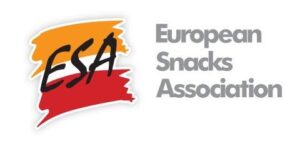
ESA - European Snacks Association
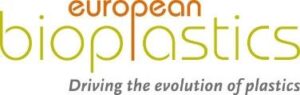
EUBP - European Bioplastics
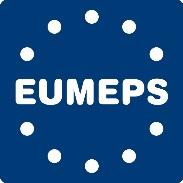
EUMEPS - European Manufacturers of Expanded Polystyrene
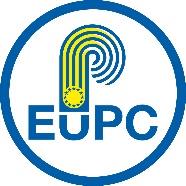
EuPC - European Plastics Converters
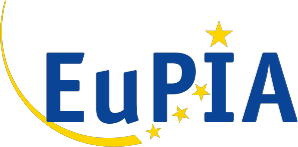
EUPIA - The European Printing Ink Association
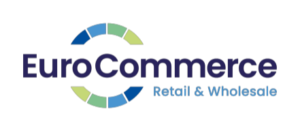
EUROCOMMERCE
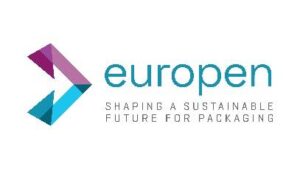
EUROPEN - The European Organization for Packaging and the Environment
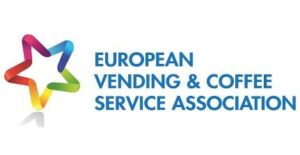
EVA - European Vending & Coffee Service Association
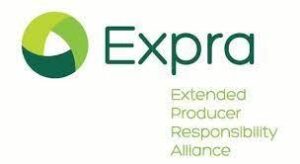
EXPRA - Extended Producer Responsibility Alliance
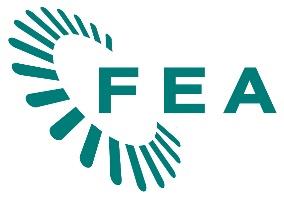
FEA - European Aerosol Federation
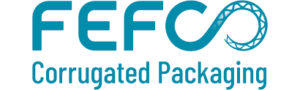
FEFCO - The European Federation of Corrugated Board Manufacters
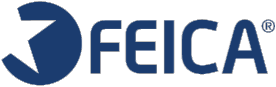
FEICA - Association of the European Adhesive & Sealant Industry
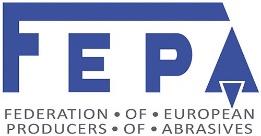
FEPA - Federation of European Producers of Abrasives

FFI - Fachverband Faltschachtel-Industrie e. V.
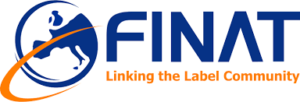
FINAT - The association for the European self-adhesive labelling and adjacent narrow-web converting industries
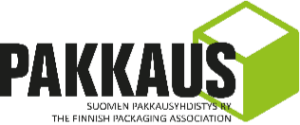
FPA - Finnish Packaging Association
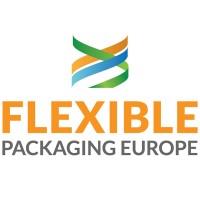
FPE - Flexible Packaging Europe
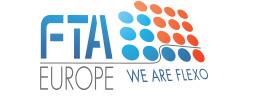
FTA EUROPE
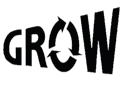
GROW International - The European organisation of lightwood packaging manufacturers
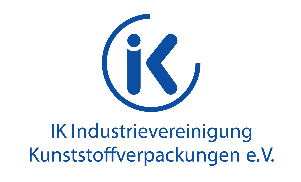
IK - Industrievereinigung Kunststoffverpackungen
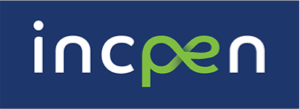
INCPEN - The Industry Council for Packaging & the Environment
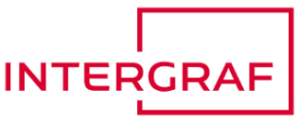
INTERGRAF - European federation for print & digital
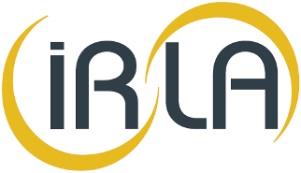
IRLA - International Release Liner Association
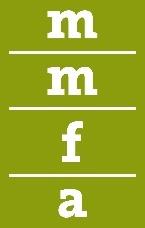
MMFA - Multilayer Modular Flooring Association
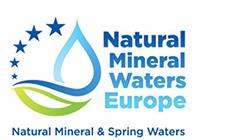
NMWE - Natural Mineral Waters Europe
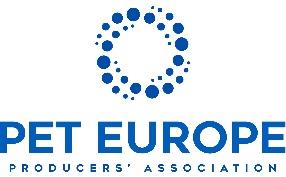
PET Europe - Producers’ Association
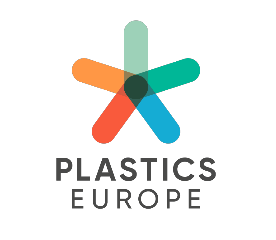
Plastics Europe
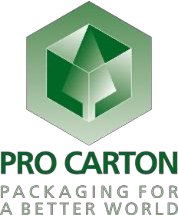
Pro Carton - Association of European Cartonboard and Carton Manufacturers
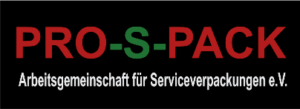
PRO-S-PACK e.v.

RISE - Research Institutes of Sweden
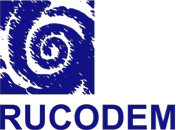
RUCODEM - Romanian Union of Cosmetics and Detergents Manufacturers
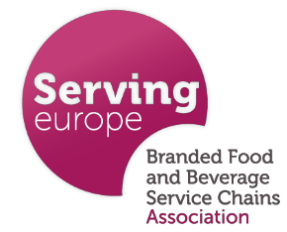
Serving Europe - Branded Foopad and Beverage Service Chains Association
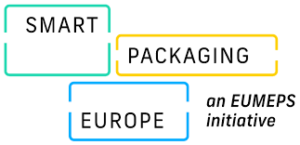
SPE - Smart Packaging Europe
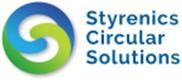
SCS - Styrenics Circular Solutions
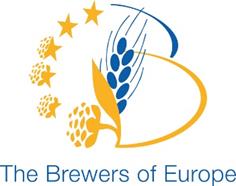
The Brewers of Europe
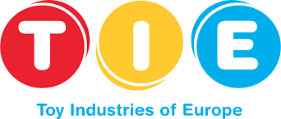
TIE - Toys Industries Europe
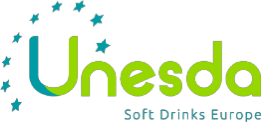
UNESDA - Union of European Beverages Association
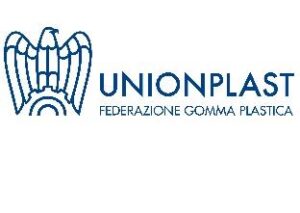
Unionplast - The Italian Plastics Converting Association
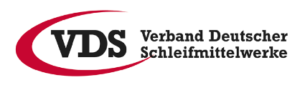
VDS - Verband Deutscher Schleifmittelwerke
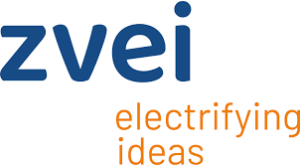
ZVEI e.V. - Electro and Digital Industry Association
For more information contact:
DNU - Treuhandbuero: Ms. Tanja Hamzei (Marketing Manager) tanja.hamzei@dnu.eu
October 2022
IRLA Position on PPWD
Extracted email text / see full version in PDF below
IRLA, International Release Liner Association, is fully in accordance with the principles of the new Packaging and Packaging Waste Regulation as it recently became published unofficially. We welcome the protection of the environment and of the human health as an undisputable superior goal.
However, we recognise certain issues with the use of a “negative list of packaging characteristics” as annexed. The present list contains definitions of material properties related to the currently available recycling methods, together with just plain materials without considering ongoing and future developments that will allow recycling of packaging materials comprising such characteristics.
Silicone coated papers are a necessary product used in a very wide range of applications in daily life. This includes carriers for self-adhesive labels, self-adhesive tapes (used in many markets from Automotive to Aerospace, Consumer, Electronics and Medical), Bakery release papers, Personal Care, Composite manufacturing and Construction Industries. The release liners are a small but essential component in a wide range of products and processes.
Silicone coated papers can be recycled (ref ISRI1), and are already recycled today on an industrial scale. As an industry association we are constantly seeking to further increase the rate of recycling of our release liners.
We therefore disagree with the proposal to include silicone coated papers in the “negative list of packaging characteristics”, because not only can silicone papers actually be recycled today, but in our opinion, it would hinder the entire value chain to develop future (and even better) recycling solutions.
IRLA, the International Release Liner Association, is the organisation gathering and representing the producers of siliconised release papers and films as well as members of the respective supply chain.
1) ISRI, Institute of Scrap Recycling Industries (Washington, DC), is an international organisation, that recently announcedsiliconised papers as recyclable. https://www.isri.org/news-publications/news-details/2022/04/19/public-notice-isri-board-approves-changes-to-the-guidelines-for-paper-stock
For more information contact:
DNU - Treuhandbuero: Ms. Tanja Hamzei (Marketing Manager) tanja.hamzei@dnu.eu
October 2020
SILICONE MIGRATION FROM SILICONE COATED RELEASE LINERS & AND THE POTENTIAL IMPACT THIS MAY HAVE ON THEIR APPLICATION
(A.Knott IRLA & Dr.R. Wilken IFAM)
WHAT ARE SILICONE RELEASE LINERS? Silicone Release Liners are an essential part of many ‘sticky’ or self-adhesive products. The Release Liner performs a number of essential roles in protecting and supporting self-adhesive materials, allowing their subsequent processing (such as die-cutting), before finally ‘releasing’ the self-adhesive material to be used their final application. The most common applications are for self-adhesive labels and tapes where there often needs to be a protective liner, but release liners are also used in a wide range of other applications where the applied material is only ‘sticky’ for a specific part of the process (such as in composite release liners).
WHAT IS SILICONE MIGRATION? The silicone release coating is a very thin layer of an elastomeric silicone rubber on the surface of the release liner. The silicone needs to be applied as a liquid, before being crosslinked to form the final silicone elastomer. They can be applied as solvent dispersions, water-based emulsions, or (most commonly) as a mixture of silicone fluids referred to as ‘solventless silicone coatings’. Regardless of the physical form they all need to be crosslinked to form the final silicone elastomer using heat or UV radiation.
The release coatings are designed such that all of the polymers will crosslink to form the final elastomeric coating, but there is always the risk that there might be a small proportion of unreacted silicone polymers present in the final release coating (either because they did not successfully react into the elastomer, or because they lack the functional groups which enable them to react into the silicone elastomer).
The presence of these unreacted silicone polymers in the final release coating means that there is a potential risk of them migrating beyond coating. Typically, such migration would initially be to the silicone surface and then from there, migration onto and into the material in contact with the silicone such as the Pressure Sensitive Adhesive (PSA), or the base substrate.
In order to better understand and characterize the level of silicone migration from a release liner and the subsequent impact this migration could have, a series of studies were completed under the leadership of IFAM (Fraunhofer Institute). Their initial evaluations on typical, well crosslinked, silicone release liners showed that for such ‘well-crosslinked’ release coatings(ref 1,2&3), only very low levels of silicone migration could be expected (equivalent to 5-10% of the contaminated surface covered). Only where level of crosslinking was demonstrably lower could there be more significant levels of contamination.
WHAT MIGHT BE THE IMPACT OF SILICONE MIGRATION? The impact of silicone migration on performance of other materials has historically been perceived as having two main types of effect: (a) Reduction in adhesion performance on contaminated surfaces (typically the adhesion of a Pressure Sensitive Adhesive (PSA) to a contaminated surface or contaminated PSA surface to another surface but could also be the adhesion of a coating/paint to a contaminated surface), and (b) Interference with wetting behaviour of materials on the contaminated surface (e.g. printing performance on a contaminated surface, or wetting of a coating).
ADHESION - In order to better understand and characterize this impact of silicone migration, the same series of studies under the leadership of IFAM, ran a series of practical evaluations(ref4,5),. These included measurements to correlate the level of silicone migration with the impact they could have on adhesive performance. The focus in this case was that of the automotive industry where the team wanted to characterize the scale of impact of silicone migration on adhesion of PSA’s to contaminated car surfaces as well as adhesion of laquers and paints to car surfaces. Through controlled contamination of surfaces and adhesion testing, they were able to demonstrate that in order to significantly reduce adhesion performance on a car body it would require a very high level of silicone migration. This can be clearly seen from the following graph where a range of PSA’s used in automotive applications were tested against silicone contaminated surfaces. The level of silicone contamination was determined using X-ray Photoelectron Spectroscopy (XPS), where the atomic% Si can be measured and converted into silicone coverage (x4, assuming all Si is present as silicone). After a small initial reduction in adhesion at very low levels of surface contamination, there is little impact of silicone contamination on adhesion until a very high level of surface coverage is reached (around 80% silicone surface coverage).
The impact of silicone contamination on adhesion of other materials was also studied. This included an evaluation of the adhesion of a water based lacquer used widely in the automotive industry, to a standard corrosion treated metal surface used to represent a car body (known as KTL-steel). Here the impact of silicone contamination was even weaker than for PSA adhesion, with even very high levels of silicone contamination showing no impact at all on the paint adhesion (as characterized by the automotive test method for paint adhesion).
WETTING - As a further step, the study also included evaluations on the impact of silicone migration on ‘wetting’ of materials (such as paints/lacquers and printing inks), to contaminated surfaces. This included evaluation of the coating performance of a water based automotive lacquer (same as had been used for adhesion testing), onto metal surfaces contaminated with silicone. The metal surface was a standard corrosion treated surface (KTL-steel), and the visible ‘coating defects’ were assessed in terms of number and size. The results showed that even at quite low levels of silicone contamination (>20% surface coverage), there was evidence of ‘coating defects’ for the most ‘sensitive’ lacquers, although at the very low levels of surface contamination (around 10%), there were no defects.
SUMMARY & CONCLUSIONS - Migration of silicone species from silicone release liner is always a possibility where the silicone coating is brought into contact with other surfaces. Even if completely crosslinked there is always the chance of some migration of silicone species. What this work has highlighted, though, is that under normal circumstances, with a well crosslinked release liner, such low levels of silicone migration should not be enough to have an impact on the subsequent performance of the materials involved. In terms of the impact on adhesion performance, only a very high level of silicone migration could have any significant
impact which could only occur where the release coating had not been sufficiently crosslinked. In terms of the impact on ‘wetting’ defects it was evident that silicone migration was more of a concern and showed an impact at much lower levels, but even here, provided that the level of crosslinking of the silicone release coating was sufficient, there should still not be any significant impact.
The overall conclusion is that provided the level of silicone crosslinking is sufficient (equivalent to a silicone ‘extractables’ level of less than 3%), there should be no significant impact on either ‘adhesion or ‘wetting’ of materials that come into contact with the silicone release liners.
References
- Wilken, R. & Henneman, O. - Siliconkontaminationen (Teil 1); Qualitative und Quantiative Bestimmung - Adhäsion Kleben und Dichten – 2002, Vol 1-2, p.36-39
- Wilken, R. & Henneman, O. - Siliconkontaminationen (Teil 2); Folgen bei Haftklebungen. - Adhäsion Kleben und Dichten – 2002, Vol 3, p.36-39
- Wilken, R. & Henneman, O. - Siliconkontaminationen (Teil 3); Warum klebt es trotzdem? - Adhäsion Kleben und Dichten – 2002, Vol 4, p.36-39
- Wilken, R, Buchbach, S. & Henneman, O. - Wann schädigen Silicon-kontaminationen Haftklebungen und Lackierungen? - Adhäsion Kleben und Dichten – 2005, Vol 1-2, p.26-29
- Wilken, R. & Henneman, O. - Siliconkontaminationen; Transfer und Wanderung auf Haftklebstoffoberflächen. - Adhäsion Kleben und Dichten – 2005, Vol 3, p.25-29
November 2019
An improving picture for the recycling of release liners, although removing further barriers would maximize the opportunity
Paul Ashford, Managing Director, Anthesis-Caleb
Regulatory and sustainability advisors to the International Release Liner Association (IRLA)
Recycling options for both papers and films
There have been numerous initiatives to promote and enable the recycling of siliconized release papers and films over recent years, with varying degrees of success. These have been promoted by companies such as UPM Raflatac, through their Rafcycle concept dealing with both release papers and films, Cycle4Green and Channeled Resources.
While siliconized films can be simply re-ground and granulated to offer a PET or polypropylene (PP) feedstock for reuse as release film or downcycled applications, release papers seem, at first glance, to be more challenging because the papers are silicone coated and the silicone has to be removed before re-using the cellulose fibres. However, the paper can be pulped and, with a chemical treatment similar to that used for newsprint, the silicones can be released and separated through a flotation process, leaving the high quality fibre to be recycled into a choice of paper products from release liners to label facings or other graphical papers.
Siliconized papers – economics hold the key
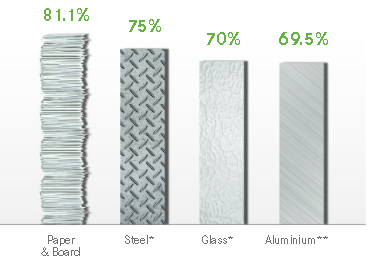
Overall, paper recycling is one of the most efficient recycling processes with paper and board outstripping rates for other basic materials.
However, on average, the fibre can only be recycled between 3-4 times before its integrity is lost, leaving a theoretical maximum sustainable recycling rate of ~79%.
While the technical criteria are well-established, the fact that siliconized papers require special treatment means that there needs to be a concentrated supply to feed the process. Where this is the case, the operation can be cost neutral with the profit margin being created by avoided waste disposal costs. This can be a particularly important in Europe where charges can be quite significant.
However, as soon as supplies are geographically scattered, the costs of collection can become prohibitive. As a result, the main investment opportunities focus around facilities where significant volumes of release papers are available.
As an example, Henkel partnered with UPM in 2016 to recycle more than 400 tonnes of siliconized glassine label liner waste at its Wassertrüdingen facility in Germany. This represented around 20 truck loads of liner waste. More recently, Techlan, a company based in South Wales, received the first grant awarded from the £6.5 million Circular Economy Fund, set up in South Wales by the Welsh Assembly. The grant is claimed to make it possible for Techlan to double its capacity in the recycling of Waste Release Liner and provide a wider range of product sizes to the market. The basis for the Techlan success in Swansea is the access that it has to release liners used for the manufacture of pre-impregnated composites in the locality.
For release paper economics, colour matters!
There has been a long-standing discussion within the release liner industry about the colour of release papers. Some of those specifying believe that darker colours – particularly shades of brown are more forgiving than white products. However, this creates a challenge in that darker papers, when mixed with white sources tend to visually degrade the recycled products leading to a loss of value in the recycled material. This in turn, can tip the balance of the underlying economics and reduce the attractiveness of the recycling option. Although the pulp can be bleached, this adds a further process step and associated cost. It also adds to the chemical footprint which is, by definition, less sustainable. The other alternative is to seek to sort the waste into its respective colours, but this also adds a handling step with its associated costs
The IRLA membership is keen to see as high a level of standardization as possible to maximize the possibilities for economic recycling. With the European Commission now moving into the second phase of its Circular Economy Action Plan, the main initiative relating to paper recycling is covered under the ‘ImpactPaperEC’ initiative which is seeking to promote best practice on paper recycling. IRLA wants to be sure that release paper recycling plays its part in fulfilling these objectives.
For more information contact:
Tanja Hamzei at tanja.hamzei@dnu.eu
or
Paul Ashford at paul.ashford@anthesisgroup.com